技術(shù)概況
制備氮化鋁陶瓷制品的工藝流程一般由原料處理、粉體合成、粉料處理、成形、生坯處理,燒結(jié)和陶瓷體處理等環(huán)節(jié)組成。
氮化鋁陶瓷制備工藝的類型主要是按合成、成型和燒結(jié)的不同方法和次序區(qū)分的。
1、反應(yīng)燒結(jié)(RS)
反應(yīng)燒結(jié)氮化鋁是把Si粉或Si粉與Si3N4粉的混合物成形后 ,在1200 ℃左右通氮氣進行預(yù)氮化,之后機械加工成所需件,最后在 1400
℃左右進行最終氮化燒結(jié)。在此過程中不需添加助燒劑等,因此高溫下材料強度不會明顯降低。同時,反應(yīng)燒結(jié)氮化鋁具有無收縮特性,可制備形狀復(fù)雜的部件,但因制品致密度低70
%~90 % ,存在大量氣孔,力學(xué)性能受到較大的影響。
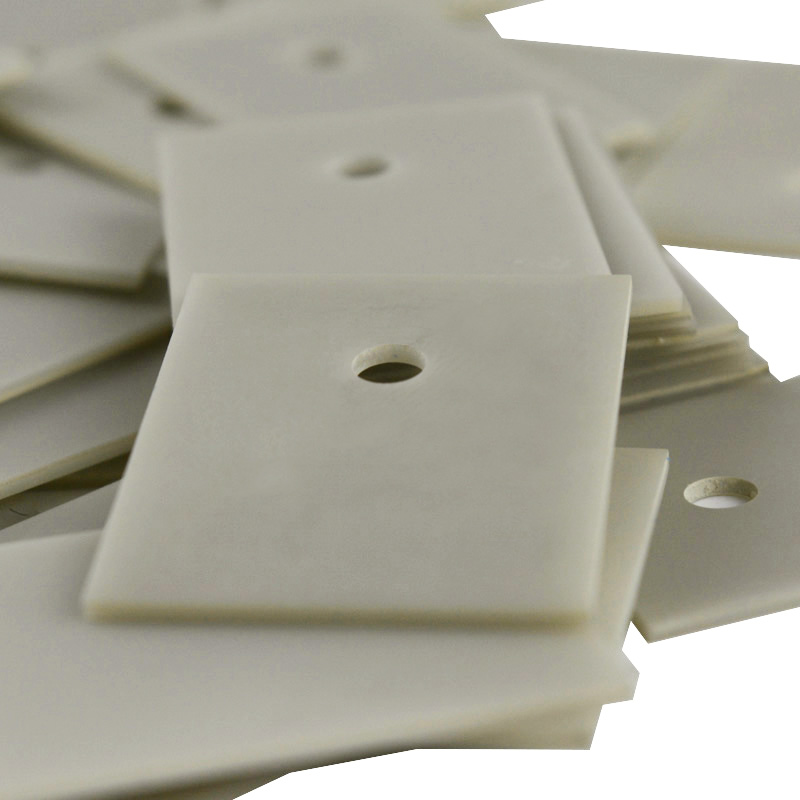
2、常壓燒結(jié)( PLS)
常壓燒結(jié)氮化鋁是以高純、超細(xì)、高α相含量的氮化鋁粉末與少量助燒劑混合,通過成形、燒結(jié)等工序制備而成。在燒結(jié)過程中,α相向液相溶解, 之后析出在β-
Si3N4晶核上變?yōu)棣? Si3N4,這有利于燒結(jié)過程的進行。燒結(jié)時必須通入氮氣 ,以抑制Si3N4的高溫分解。常壓燒結(jié)可獲得形狀復(fù)雜、性能優(yōu)良的陶瓷
,其缺點是燒結(jié)收縮率較大 ,一般為16 %~26 %,易使制品開裂變形。
3、重?zé)Y(jié)(PS)
將反應(yīng)燒結(jié)的Si3N4燒結(jié)坯在助燒劑存在的情況下,置于氮化硅粉末中,在高溫下重?zé)Y(jié),得到致密的Si3N4制品。助燒劑可在硅粉球磨時引入,也可用浸漬的方法在反應(yīng)燒結(jié)后浸滲加入。由于反應(yīng)燒結(jié)過程中可預(yù)加工,在重?zé)Y(jié)過程中的收縮僅有6
%~10 %,所以可制備形狀復(fù)雜,性能優(yōu)良的部件。
4、熱壓燒結(jié)(HP)
把氮化鋁粉末與助燒劑置于石墨模具,在高溫下單向加壓燒結(jié)。由于外加壓力提高了燒結(jié)驅(qū)動力,加快了α→β轉(zhuǎn)變及致密化速度。熱壓法可得到致密度大于95
%的高強氮化鋁陶瓷,材料性能高,且制造周期短。但是這種方法只能制造形狀簡單的制品 ,對于形狀復(fù)雜的部件加工費用高 ,而且由于單向加壓 ,組織存在擇優(yōu)取向
,使性能在與熱壓面平行及垂直方向有差異。
5、氣壓燒結(jié)( GPS)
氣壓燒結(jié)是把Si3N4壓坯在5~12MPa的氮氣中于1800~2100 ℃下進行燒結(jié)。由于氮氣壓力高 ,從而提高了Si3N4的分解溫度
,有利于選用能形成高耐火度晶間相的助燒劑 ,來提高材料的高溫性能。
6、熱等靜壓法( HIP)
將氮化鋁及助燒劑的混合物粉末封裝到金屬或玻璃包套中 ,抽真空后通過高壓氣體在高溫下燒結(jié)。常用的壓力為200MPa ,溫度為
2000℃熱等靜壓氮化硅可達(dá)理論密度,但它工藝復(fù)雜,成本較高。
近年來還發(fā)展了其他一些燒結(jié)和致密化工藝,如超高壓燒結(jié)、化學(xué)氣相沉積、爆炸成形等。
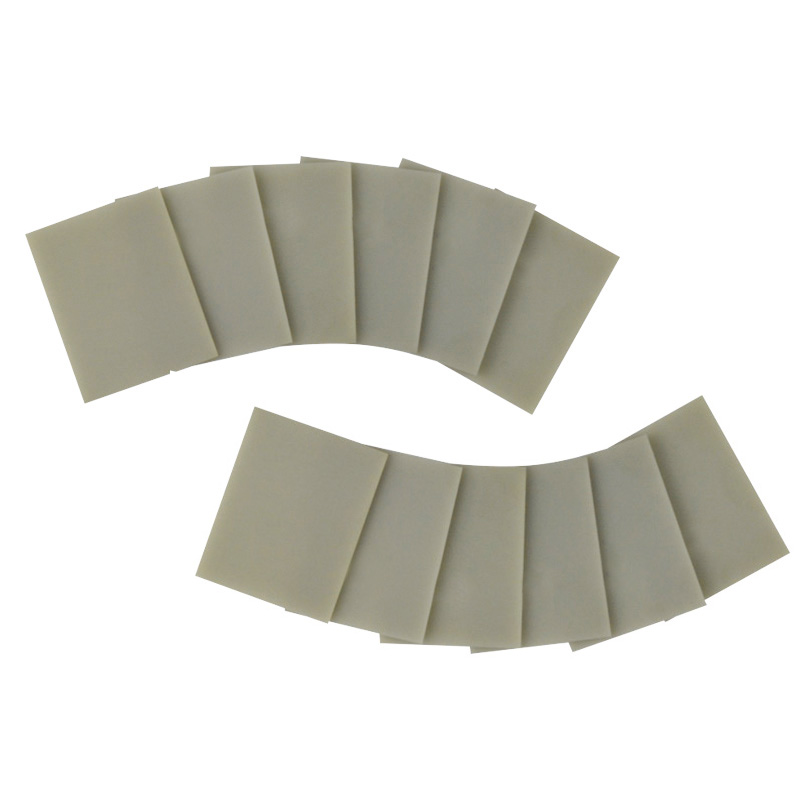
氮化鋁陶瓷國內(nèi)市場簡述
氮化鋁陶瓷主要是作為高溫結(jié)構(gòu)及工程材料被研究、開發(fā)、應(yīng)用。氮化硅制品已經(jīng)形成商品,投放市場,主要用在機械、化工、冶金、航空、能源、建材、半導(dǎo)體等工業(yè)上,作某些設(shè)備及產(chǎn)品的零部件。氮化鋁年需求量(國內(nèi))在27萬噸以上,而國內(nèi)生產(chǎn)量僅10萬噸左右;氮化鋁作為結(jié)構(gòu)鋼的增氮劑,能提高鋼的綜合性能,年市場需求量在6萬噸以上。在鋼鐵生產(chǎn)中作為耐火材料需求量超過10萬噸;作為深加工原料如氮化鋁軸承、發(fā)動機外殼、刀具等產(chǎn)品,年需求量約6萬噸。市場前景廣闊。